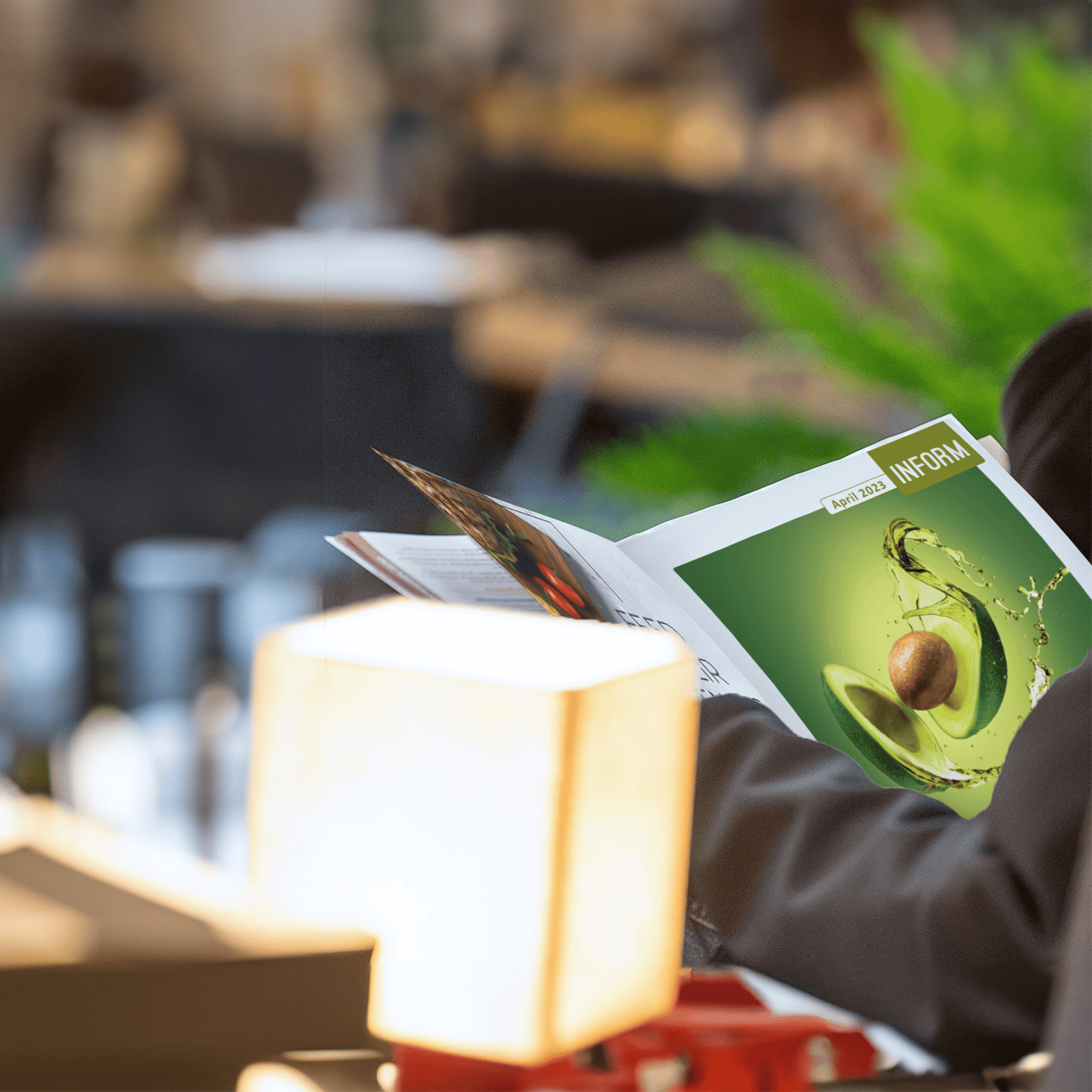
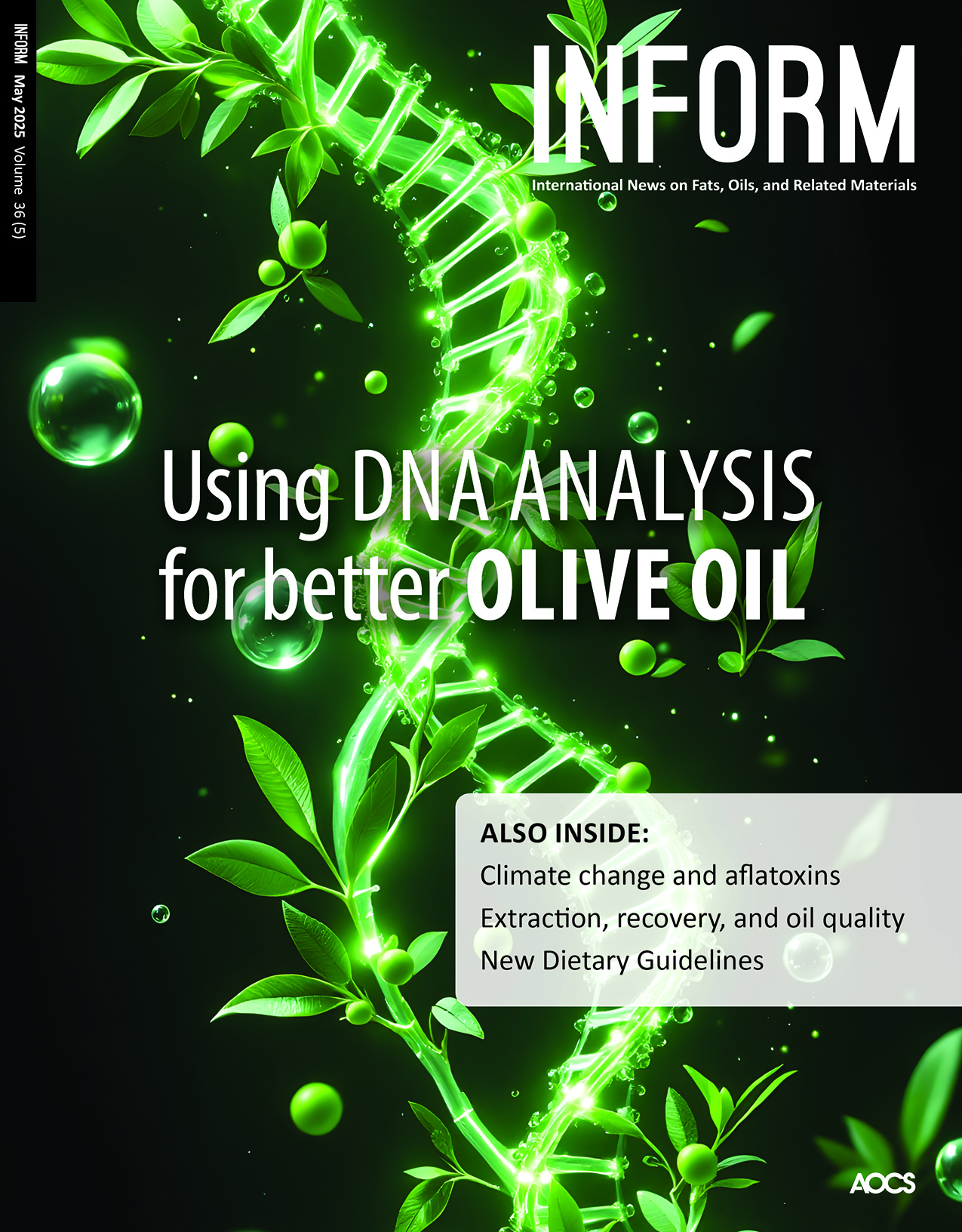
The official member magazine of AOCS
Published 10 times a year, INFORM magazine provides comprehensive reviews and original articles on such topics as:
- new analytical methods and technologies
- processing technologies that improve efficiency and sustainability
- health and nutrition
- formulation science
- critical business issues
- and many other topics
Each issue includes patent abstracts compiled by a registered US patent agent, journal references assembled by a team of experts in a variety of areas, and coverage of regulatory issues from around the globe.
Access to the full online version of INFORM magazine is only available to AOCS members. Join today for full access to INFORM.
Current issue - May 2025
Olive oil authenticity
Olive oil fraud is a significant economic concern addressed by emerging DNA based testing methods that can detect non-olive adulterants with greater specificity and sensitivity than traditional chemical analyses. Despite promising advances like a visual DNA sensor that can identify specific adulterant oils at low concentrations, challenges remain in establishing standardized DNA testing protocols that meet regulatory requirements and can distinguish between closely related olive varieties.
Aflatoxin on the rise: How climate change is reshaping food safety
Aflatoxin contamination in food crops is increasing due to climate change, as rising temperatures and irregular precipitation create favorable conditions for Aspergillus fungi growth in regions previously unaffected. Read about the actions by researchers and their recommendations for regulatory agencies to reduce this impending threat to food safety.
Impact of extraction and recovery methods on almond oil quality: A lipidomic perspective
Lipidomic analysis revealed that environmentally friendly extraction techniques produced oil with fewer oxidation markers and higher antioxidant activity than solvent extraction. These greener alternatives maintain the same fatty acid profile while eliminating the safety and environmental concerns associated with harsh solvents.
New set of Dietary Guidelines for Americans due this year
A scientific committee submitted dietary guidelines recommending more plant-based foods and less red meat, which the Trump administration is revising before final release in December 2025. Health Secretary Kennedy criticized the report as industry-influenced. The guidelines will impact food assistance programs affecting 25 percent of Americans.
INFORM SmartBrief
INFORM SmartBrief is a free weekly newsletter designed to keep you up to date on developing regulations, research, technology, and more. This e-newsletter is aggregated by an INFORM magazine staff writer, who sorts through the barrage of oils- and fats-related notifications to bring you only the most relevant news.
Subscribe now to receive valuable oils and fats news delivered to your inbox every week.