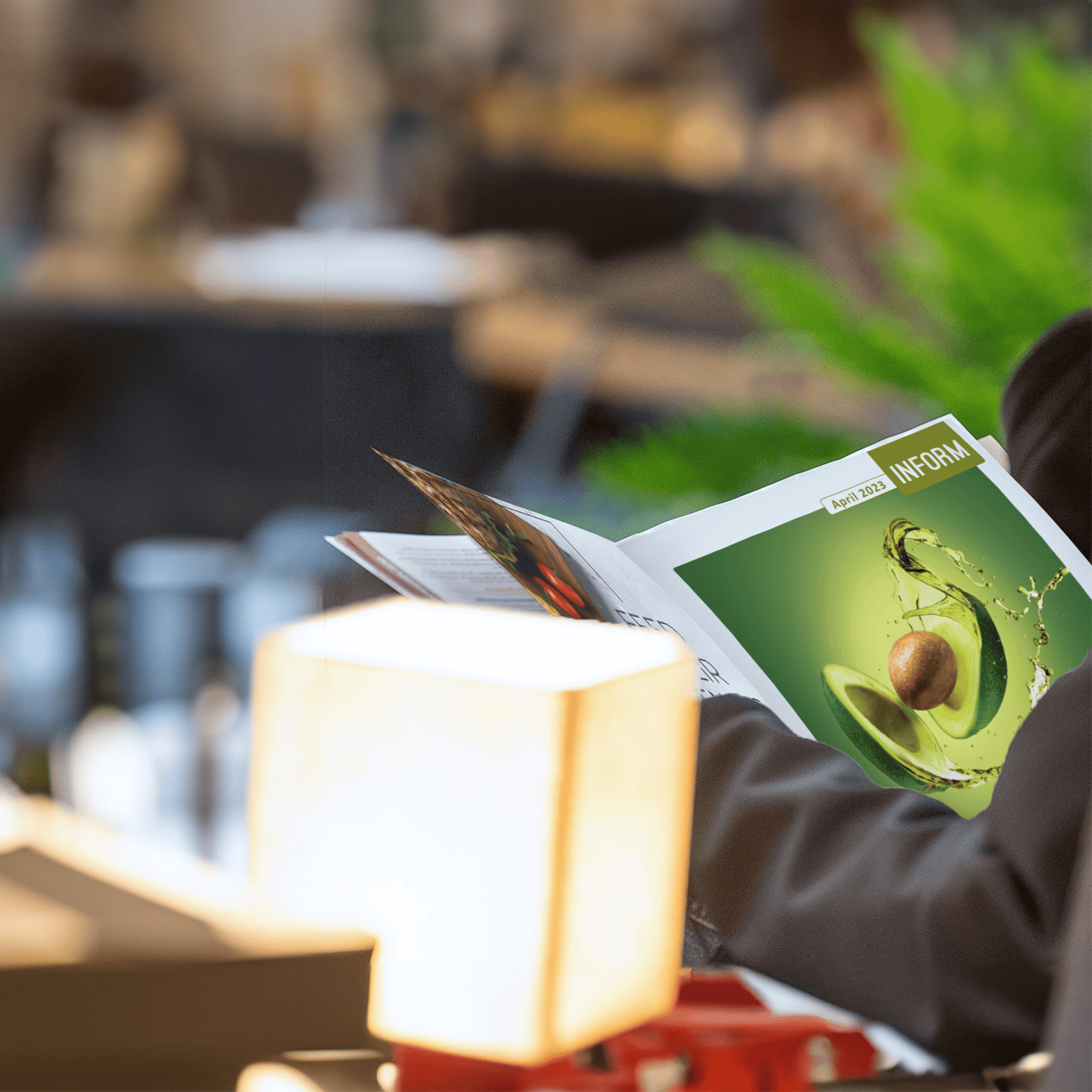
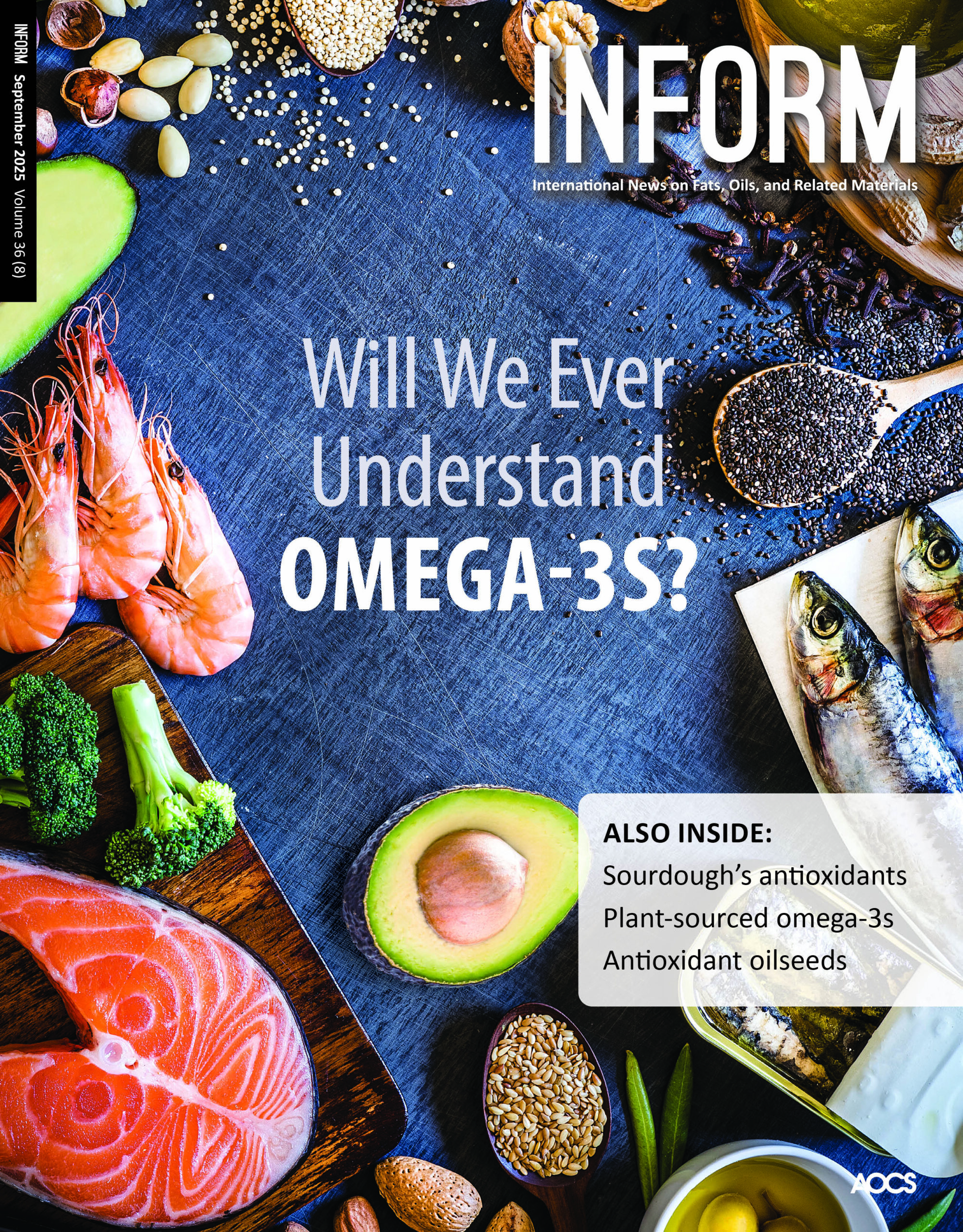
The official member magazine of AOCS
Published 10 times a year, INFORM magazine provides comprehensive reviews and original articles on such topics as:
- new analytical methods and technologies
- processing technologies that improve efficiency and sustainability
- health and nutrition
- formulation science
- critical business issues
- and many other topics
Each issue includes patent abstracts compiled by a registered US patent agent, journal references assembled by a team of experts in a variety of areas, and coverage of regulatory issues from around the globe.
Access to the full online version of INFORM magazine is only available to AOCS members. Join today for full access to INFORM.
Current issue - september 2025
(Open access)
Decades of research, still many mysteries about omega-3 fatty acids
Who benefits the most from supplementing their diets with omega-3s, men or women? Do people with metabolic disorders actually see health benefits when they up their intake? These and many other questions about the essential fatty acids remain unanswered. In this article, researchers discuss recent studies that are improving our understanding of the unique interactions of omega-3s in different people.
Sourdough rises to take on food challenges
Sourdough bread has a reputation for easier digestion and a longer shelf life than other types of bread. Researchers characterized the influence of the starter culture’s microbiome on the metabolomic profile of its sourdough bread. They discovered that differences in a bread’s metabolomic profile translate into differences in antioxidant functionality. What are the implications of their findings for food preservation and human health?
Engineered oilseed crop produces high levels of powerful antioxidant
A research team altered the ketocarotenoid biosynthesis pathway of Camelina seeds so the plant would make more astaxanthin. Their study was a success and resulted in an extracted oil with high resistance to oxidation.
Recognizing the health benefits of plant-sourced omega-3
Recent studies show that stearidonic acid (SDA) may offer similar health benefits to eicosapentaenoic acid (EPA), such as immune, joint, cognitive, and gut microbiome modulation. This article takes a glimpse at the new research exploring SDA and its potential to deliver human health benefits.
Myth-busting study shows controversial seed oils reduce
inflammation
At a recent conference for the American Society of Nutrition, scientists presented findings from a study that found omega-6s from seed oils are good for cardiometabolic health. Read this article, based on their press release, to find out more about their study methods and conclusions.
Open Access Issues
AOCS publishes two open access issues annually in April and September. You can view the latest issues here.
April 2025
Say cheese: Biotechnology and the quest for animal-free dairy
Biotech companies are modifying soybean DNA to produce casein, an animal protein, with the goal of creating animal-free dairy alternatives. However, scaling production to be commercially viable remains a significant hurdle. Beyond commercialization, these producers face regulatory approvals, consumer acceptance, and competition with traditional dairy and plant-based alternatives.
Revolutionizing edible oil refining with microfluidic networks
Microfluidic networks inspired by biology have been adapted for industrial-scale separations, offering innovative solutions for efficient processing. Now, a company has integrated enzyme-coated microfilaments to enhance the separation process. Read about how these advancements were tested for edible oil degumming, demonstrating their potential for practical applications in the industry.
Mild distillation for optimal oil quality
This article describes studies on how best to use short path distillation (SPD) to achieve shelf stability and effective contaminant removal during edible oil processing. The author compares how well mild refining conditions and SPD remove contamination from pesticides and mineral oil hydrocarbons (MOH) with the ultimate conclusion that starting with high-quality raw materials ensures the best outcome.
Enzymatic pretreatment process provides biodiesel feedstock flexibility
Addressing high free fatty acid (FFA) concentrations is a crucial aspect of biodiesel production. In this article, read about an enzymatic process that enhances fuel yield and production flexibility by significantly lowering FFA concentration in biodiesel feedstock.
INFORM SmartBrief
INFORM SmartBrief is a free weekly newsletter designed to keep you up to date on developing regulations, research, technology, and more. This e-newsletter is aggregated by an INFORM magazine staff writer, who sorts through the barrage of oils- and fats-related notifications to bring you only the most relevant news.
Subscribe now to receive valuable oils and fats news delivered to your inbox every week.