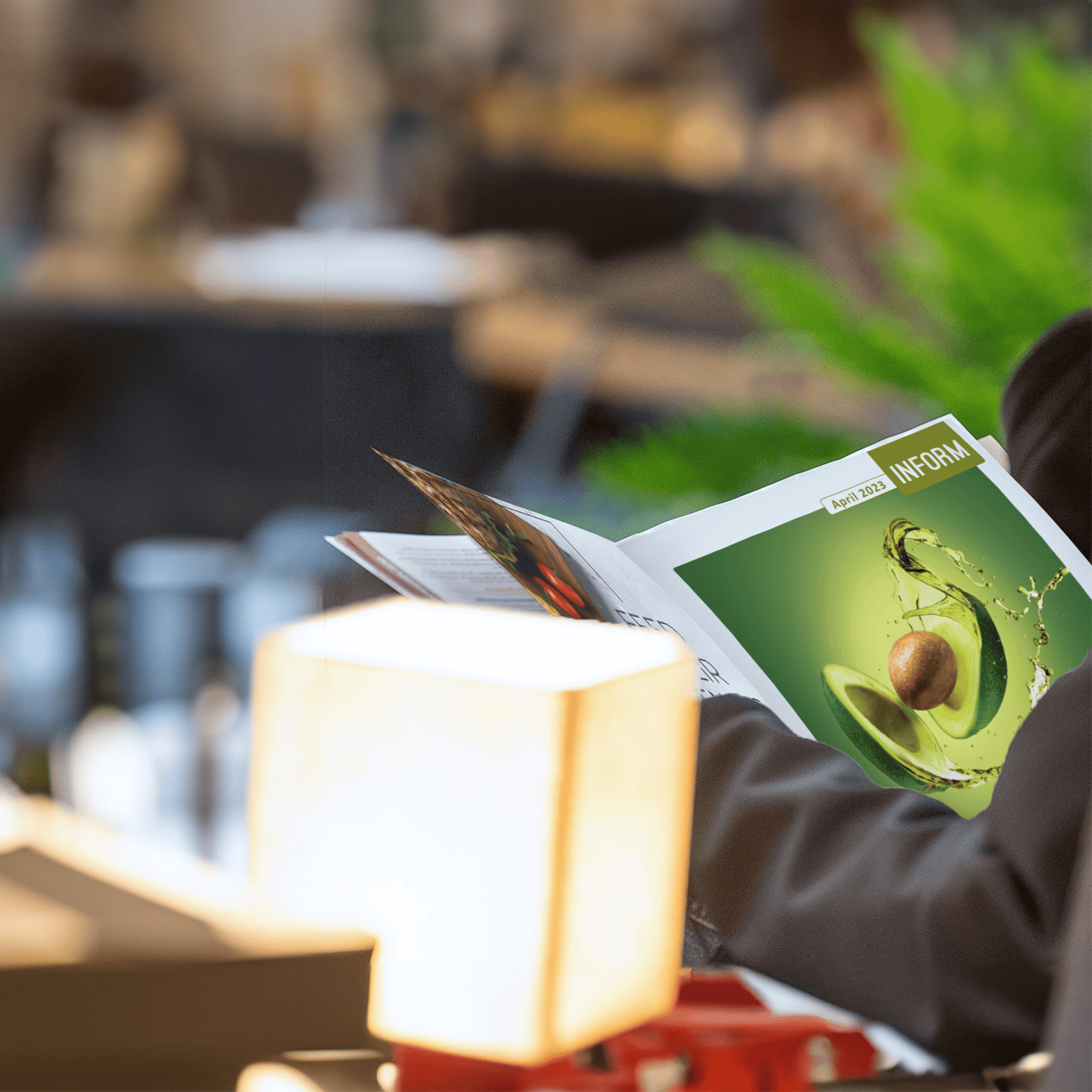
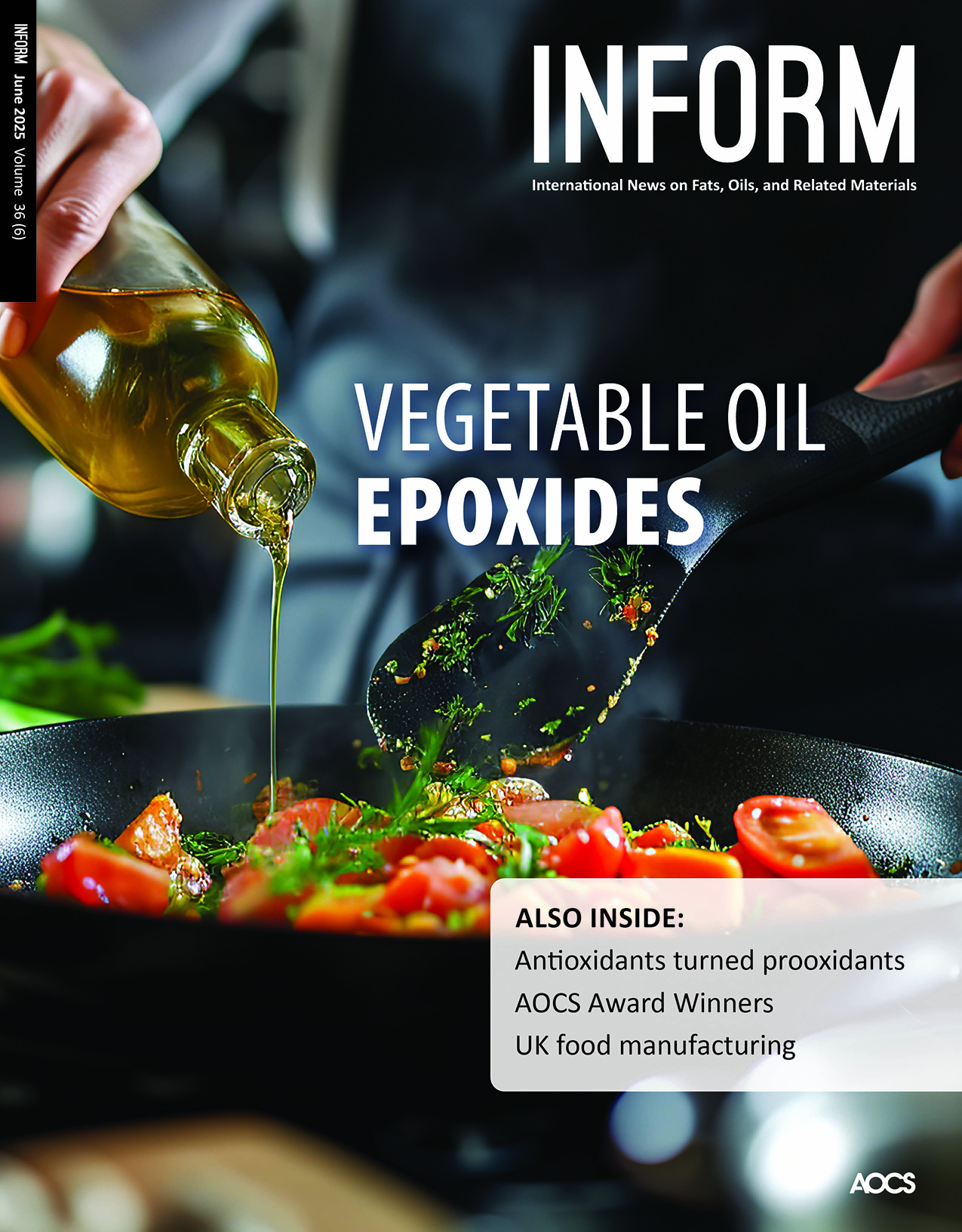
The official member magazine of AOCS
Published 10 times a year, INFORM magazine provides comprehensive reviews and original articles on such topics as:
- new analytical methods and technologies
- processing technologies that improve efficiency and sustainability
- health and nutrition
- formulation science
- critical business issues
- and many other topics
Each issue includes patent abstracts compiled by a registered US patent agent, journal references assembled by a team of experts in a variety of areas, and coverage of regulatory issues from around the globe.
Access to the full online version of INFORM magazine is only available to AOCS members. Join today for full access to INFORM.
Current issue - May 2025
From obscurity to center stage: Epoxides in lipid oxidation and human health
Epoxides are far more prevalent in lipid oxidation than previously understood, challenging established models and raising questions about their health impacts. While some epoxides play crucial roles in cell signaling, others may contribute to inflammation. Read about the research progress towards gaining a better understanding of their formation, structure, and effects in human digestive systems.
When antioxidants become prooxidants
For a long time, food manufacturers assumed that adding antioxidants to foods containing the more healthful polyunsaturated fats would slow down unwanted oxidation reactions and extend shelf-life. Read this article about studies showing that the addition of too much antioxidant can have the reverse effect and lead to an increase in oxidation reactions.
AOCS Award winners
Each year AOCS acknowledges the passion of individuals and companies who are advancing the science of fats and oils by working toward new and innovative applications. This year AOCS presented 31 awards to 43 recipients. We are proud to include this year’s awardees as part of our long-standing program. Read about them here.
Open Access Issues
AOCS publishes two open access issues annually in April and September. You can view the latest issues here.
April 2025
Say cheese: Biotechnology and the quest for animal-free dairy
Biotech companies are modifying soybean DNA to produce casein, an animal protein, with the goal of creating animal-free dairy alternatives. However, scaling production to be commercially viable remains a significant hurdle. Beyond commercialization, these producers face regulatory approvals, consumer acceptance, and competition with traditional dairy and plant-based alternatives.
Revolutionizing edible oil refining with microfluidic networks
Microfluidic networks inspired by biology have been adapted for industrial-scale separations, offering innovative solutions for efficient processing. Now, a company has integrated enzyme-coated microfilaments to enhance the separation process. Read about how these advancements were tested for edible oil degumming, demonstrating their potential for practical applications in the industry.
Mild distillation for optimal oil quality
This article describes studies on how best to use short path distillation (SPD) to achieve shelf stability and effective contaminant removal during edible oil processing. The author compares how well mild refining conditions and SPD remove contamination from pesticides and mineral oil hydrocarbons (MOH) with the ultimate conclusion that starting with high-quality raw materials ensures the best outcome.
Enzymatic pretreatment process provides biodiesel feedstock flexibility
Addressing high free fatty acid (FFA) concentrations is a crucial aspect of biodiesel production. In this article, read about an enzymatic process that enhances fuel yield and production flexibility by significantly lowering FFA concentration in biodiesel feedstock.
INFORM SmartBrief
INFORM SmartBrief is a free weekly newsletter designed to keep you up to date on developing regulations, research, technology, and more. This e-newsletter is aggregated by an INFORM magazine staff writer, who sorts through the barrage of oils- and fats-related notifications to bring you only the most relevant news.
Subscribe now to receive valuable oils and fats news delivered to your inbox every week.