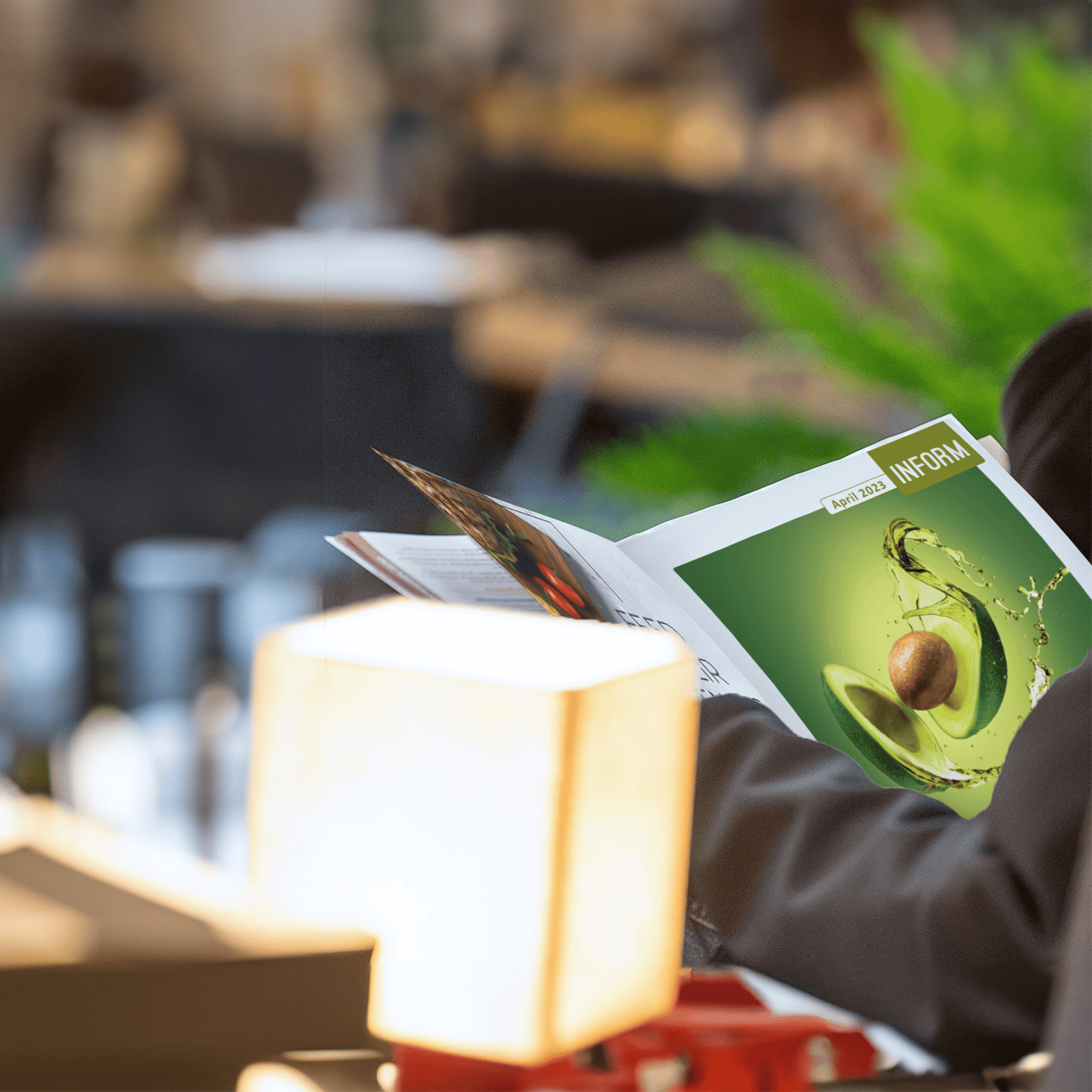
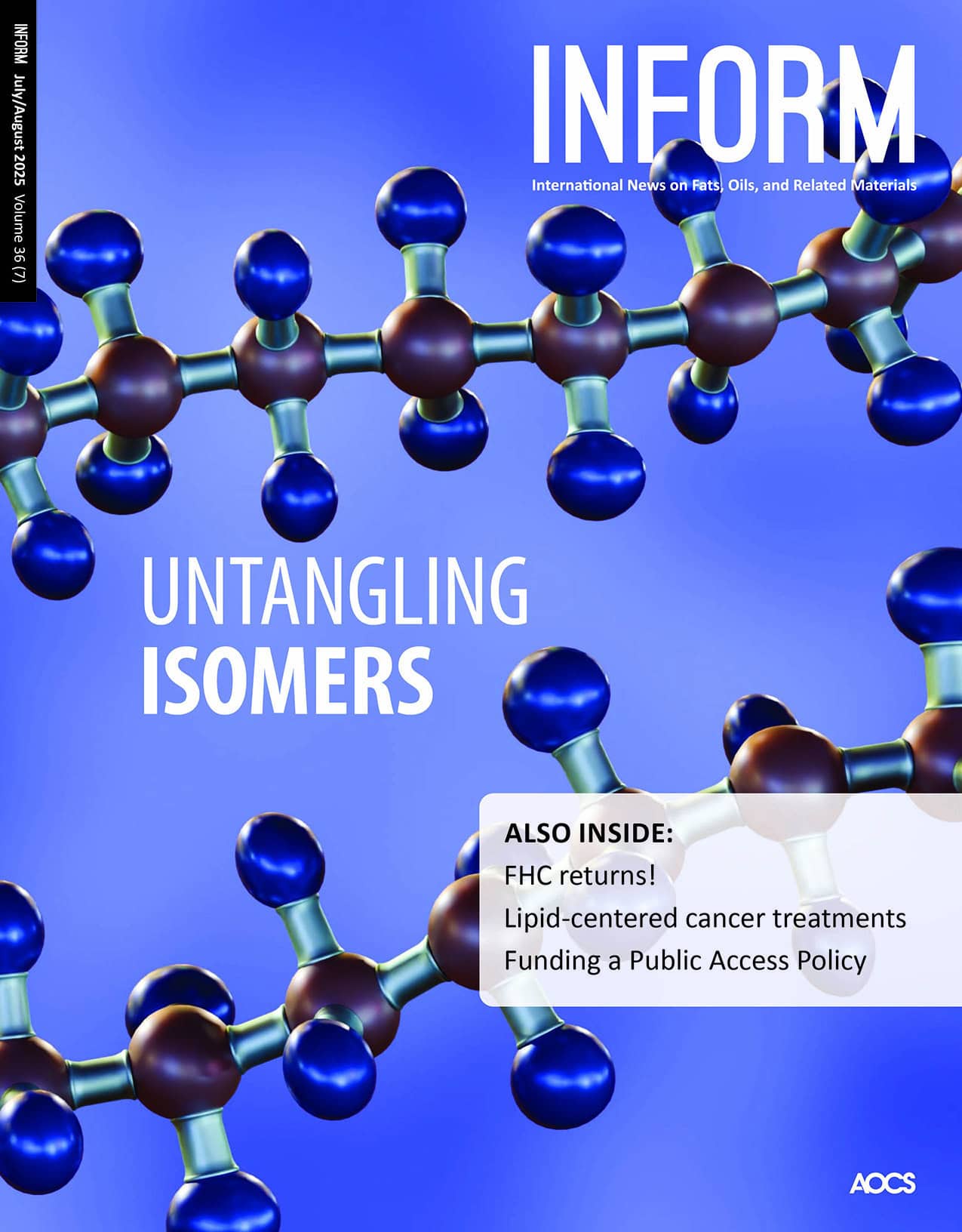
The official member magazine of AOCS
Published 10 times a year, INFORM magazine provides comprehensive reviews and original articles on such topics as:
- new analytical methods and technologies
- processing technologies that improve efficiency and sustainability
- health and nutrition
- formulation science
- critical business issues
- and many other topics
Each issue includes patent abstracts compiled by a registered US patent agent, journal references assembled by a team of experts in a variety of areas, and coverage of regulatory issues from around the globe.
Access to the full online version of INFORM magazine is only available to AOCS members. Join today for full access to INFORM.
Current issue - July/August 2025
Building more nutritious foods with lipids
To make healthy fats, researchers in Finland realized they first had to develop methods for effectively analyzing lipid isomers. A lipid’s properties are based on the location and orientation of fatty acids, but regioisomers and enantiomers of separate molecules are detected as if they were the same molecule. New methods are helping the team learn how to distinguish between them so they can determine the fate of lipid components in the human body. Read about how these researchers are using their findings to make food more nutritious and easier to digest.
Fabric & Home Care returns!
The World Conference on Fabric & Home Care was once a long-standing tradition of AOCS. This year the conference returned, in a post-pandemic format, as The Fabric & Home Care Forum. Read about the key insights gained from thoughtful discussions by executive leaders on the science of sustainability and safety in the industry. And do not miss the next Forum at the Hilton Chicago in 2027.
Experimental treatment uses engineered fat cells to “starve” tumors
A team of scientists recently developed a cancer therapy targeting fatty acid metabolism. Adipose manipulation transplantation (AMT), as it is called, involves genetically engineering white adipose tissue into beige tissue. The engineered cells starve tumors by consuming the fatty acids and glucose necessary for growth. The article describes their proof-of-principle for the therapeutic approach.
Lysosomal lipid peroxidation and cancer cell death
This feature article describes another potent weapon against cancerous tumors. By exploiting the mechanisms of lipid peroxidation in phospholipids containing polyunsaturated fatty acids, researchers have another tool to fight drug-tolerant cancer cells.
A high-oleic palm oil alternative by microalgae fermentation
Hybridized palms successfully produce high-oleic oil, but they require expensive, assisted pollination that limits economic viability. In this story, researchers describe microbial oil production that eliminates the need for tropical arable land, reduces water usage compared to traditional palm cultivation, and can be implemented in non-tropical regions to reduce transportation emissions and supply chain risks while addressing deforestation concerns.
Open Access Issues
AOCS publishes two open access issues annually in April and September. You can view the latest issues here.
April 2025
Say cheese: Biotechnology and the quest for animal-free dairy
Biotech companies are modifying soybean DNA to produce casein, an animal protein, with the goal of creating animal-free dairy alternatives. However, scaling production to be commercially viable remains a significant hurdle. Beyond commercialization, these producers face regulatory approvals, consumer acceptance, and competition with traditional dairy and plant-based alternatives.
Revolutionizing edible oil refining with microfluidic networks
Microfluidic networks inspired by biology have been adapted for industrial-scale separations, offering innovative solutions for efficient processing. Now, a company has integrated enzyme-coated microfilaments to enhance the separation process. Read about how these advancements were tested for edible oil degumming, demonstrating their potential for practical applications in the industry.
Mild distillation for optimal oil quality
This article describes studies on how best to use short path distillation (SPD) to achieve shelf stability and effective contaminant removal during edible oil processing. The author compares how well mild refining conditions and SPD remove contamination from pesticides and mineral oil hydrocarbons (MOH) with the ultimate conclusion that starting with high-quality raw materials ensures the best outcome.
Enzymatic pretreatment process provides biodiesel feedstock flexibility
Addressing high free fatty acid (FFA) concentrations is a crucial aspect of biodiesel production. In this article, read about an enzymatic process that enhances fuel yield and production flexibility by significantly lowering FFA concentration in biodiesel feedstock.
INFORM SmartBrief
INFORM SmartBrief is a free weekly newsletter designed to keep you up to date on developing regulations, research, technology, and more. This e-newsletter is aggregated by an INFORM magazine staff writer, who sorts through the barrage of oils- and fats-related notifications to bring you only the most relevant news.
Subscribe now to receive valuable oils and fats news delivered to your inbox every week.